Climate change, energy costs and energy security have become increasing concerns over the last decade. This has forced industries to prioritise efficiency, which in turn is driving a demand for reliable simulation tools that help companies understand where their products can save energy.
In 2023, it was estimated that 3.2% of the UK’s total carbon emissions (12.9 megatonnes of CO2) comes from refrigeration of the food industry [1]. Although the continued efforts to decarbonise the energy sector will improve this in time, an equally powerful strategy is to reduce the demand in the first place.
Supermarkets consume approximately 3 to 4% of the annual energy in industrialised countries [2]. With approximately 30% of that energy used to power refrigeration for both chilled and frozen foods. These statistics are pushing supermarkets to address their energy consumption to reduce costs and their carbon footprint.
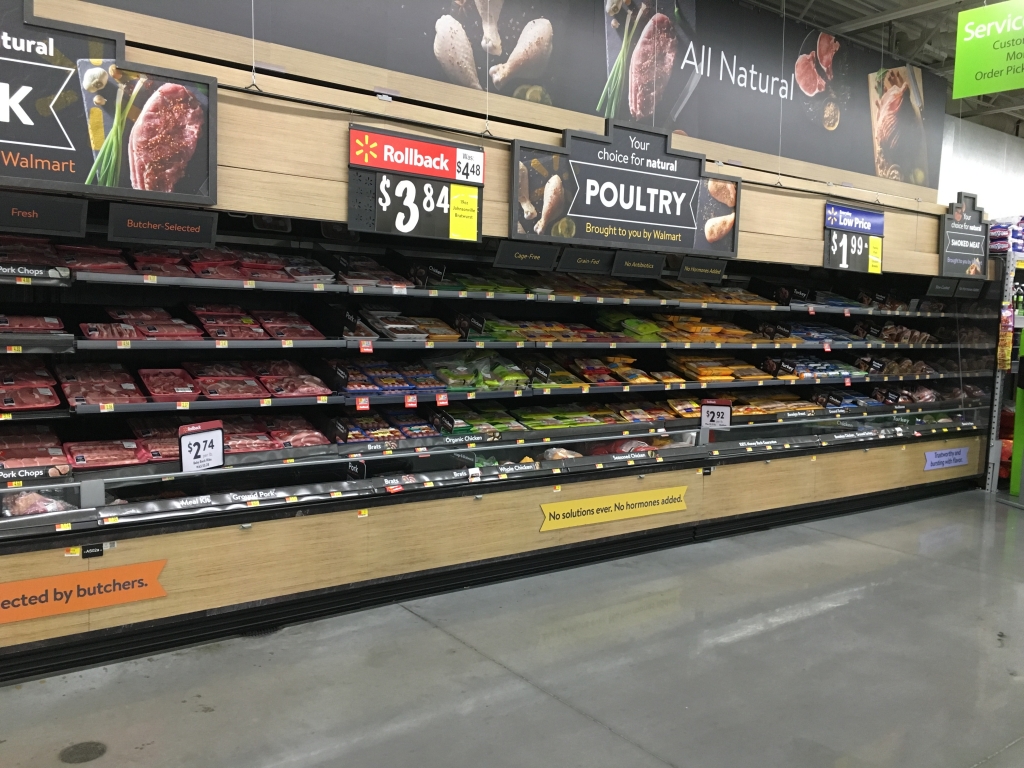
Fridge Aerodynamics
One of the most inefficient types of fridge is the traditional open-fronted chiller cabinets. A walk down any supermarket chilled aisle is typically quite a cold one, and that’s because cool air leaks from the chillers into the surrounding area, rather than cooling the products on the shelves.
These chiller cabinets are predominantly air cooled via a heat exchanger and air circulation refrigeration system. This heat exchanger is located at the bottom of the fridge and contains cool refrigerant. Fans pass warm ambient air over this heat exchanger and as the refrigerant absorbs heat, the air cools down.
This cooler air then circulates around the back of the fridge, where small slits in the back panel allow some of this air to waft through, helping to cool the main compartment of the fridge. However, the majority of this cool air moves to the top of the fridge and then falls down the front of the cabinet to the bottom.
As it does so, it absorbs heat from the food products, increasing its temperature, but keeping the food cold. Once this warmer air returns to the bottom of the fridge, the process repeats, and it is passed over the heat exchanger to cool down again.
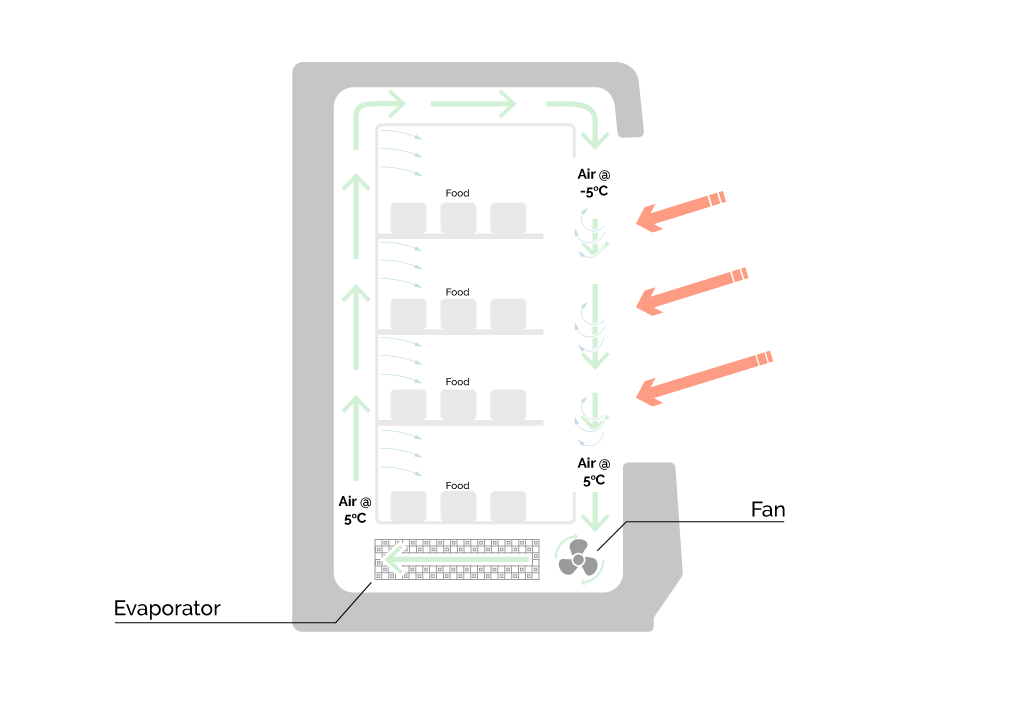
‘The air falling down the front of the cabinet forms an air curtain which effectively seals the air,’ explains Rob Rowsell, Engineering Director at Wirth Research. ‘You want the air to fall from the discharge grill into the return grill as neatly as possible. But in reality, the falling air is moving between still air on the inside and outside of the cabinet, which causes a shear layer to form on both sides.’
‘The turbulent energy in this shear layer grows as it moves down and eventually it changes from being a smooth air curtain to becoming chaotic and turbulent,’ continues Rowsell. ‘The longer the distance over which the air is turbulent and the higher the turbulence intensity, the more mixing there will be between the warm air outside the cabinet and the chilled air inside. The key to improving the efficiency of these chiller cabinets is to minimise this mixing.’
Refrigeration Simulation With HELYX
To help solve this problem, Wirth Research, an engineering consultancy born out of motorsport, decided to run Computational Fluid Dynamics (CFD) simulations using HELYX software to better understand the behaviour of this airflow.
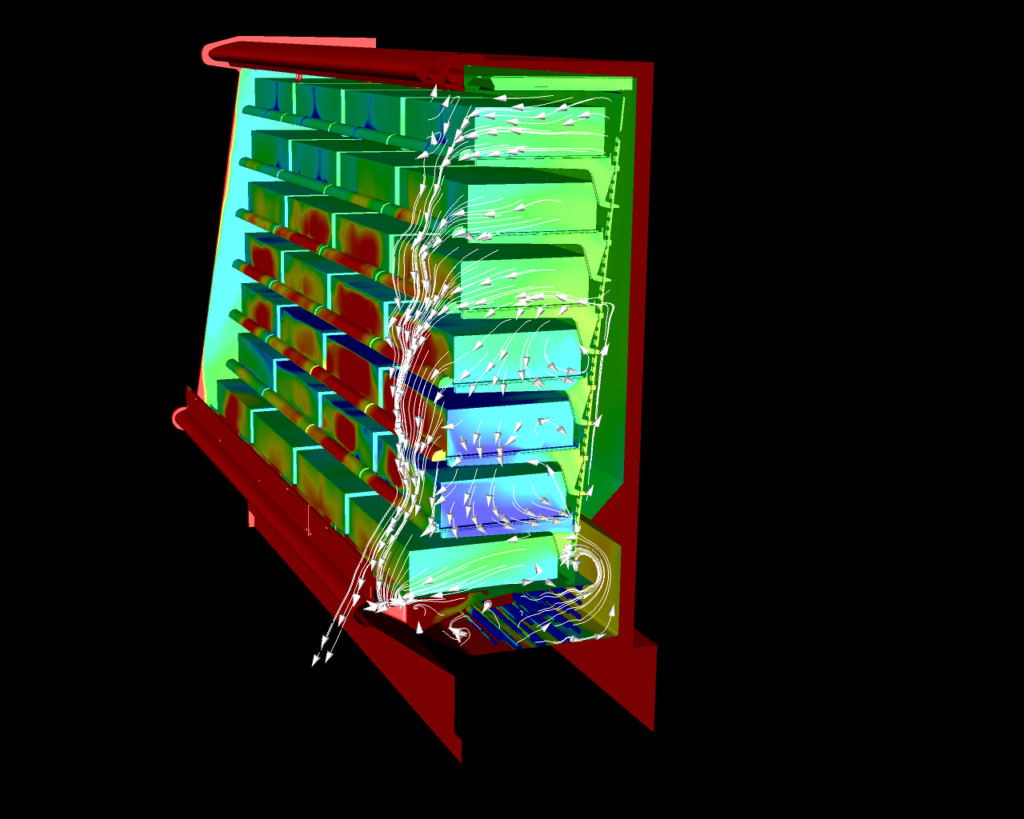
‘We stripped down a real chiller cabinet and measured each component such as the fans, panels and perforations,’ says Rowsell. ‘From this we generated a CAD model and then a CFD mesh which contained a similar number of cells to our Formula One or IndyCar models.
‘We set realistic temperature conditions and full buoyancy to account for the air density changes, and solved for both the Reynolds-Averaged Navier-Stokes (RANS) equations as well as unsteady and detached eddy simulations,’ continues Rowsell. ‘The results helped us understand the aerodynamic and thermodynamic limitations of a chiller cabinet which then led us to develop our EcoBlade solution.’
How Does The EcoBlade Work?
Wirth Research’s EcoBlade is an aerodynamic device fitted to the front of a shelf which effectively channels the air curtain as it falls from the top of the fridge to the bottom. This reduces the generation of turbulence in the shear layer and consequently minimises mixing. It consists of two plastic blades roughly 40 mm from each other, mounted to small arms at either side. These arms vary in length depending on how far the air curtain sits from the shelves.
‘The air curtain is like a long guitar string, if you pluck a guitar string there will be a large oscillation,’ highlights Rowsell. ‘But if you pinch the string half way along and then pluck it, this oscillation is much smaller. If we pinch it in multiple places, the oscillations become smaller again.’
‘The EcoBlade works on a similar principle and streamlines the air curtain. As it starts to become turbulent and widen, it passes through an EcoBlade which straightens and tidies the flow, effectively resetting it. By fitting a number of EcoBlades to the centre shelves, the flow can be controlled throughout the entire cabinet.’
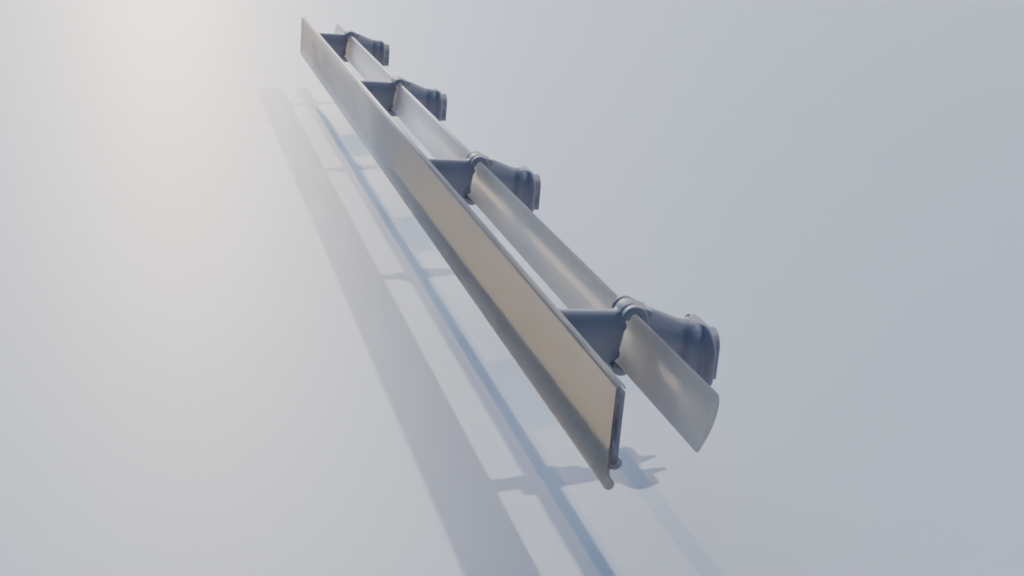
The Benefits EcoBlades Bring To Fridges
Over the last few years there have been various campaigns to fit doors to refrigerated cabinets as this can lead to energy savings of around 33% [3]. However, the total cost of this, along with the negative customer experience can often affect sales and make this an expensive undertaking for supermarkets.
‘The advantage of EcoBlade is that we can easily retrofit it to existing cabinets and it is almost invisible to the consumer, yet it improves energy use by 15 to 25%,’ says Rowsell. ‘Our more advanced TrueChill solution, which is fitted during cabinet manufacture, results in further improvements of roughly 40 to 45%, which is as good as using doors.’ From 2019 to 2021, EcoBlades were fitted across 273 Waitrose stores in the UK. This was so successful that a further rollout across another 211 stores was approved which is expected to save over one million kWh of electricity [5]. An additional benefit of EcoBlade is the improved temperature control inside the chiller cabinet which prolongs the shelf life of the products, reducing food waste and saving even more energy.
TrueChill Refrigeration
The development of EcoBlades concentrated on retrofitting existing cabinets, but Wirth took their learnings from CFD a step further and designed a fully optimised chiller cabinet called TrueChill.
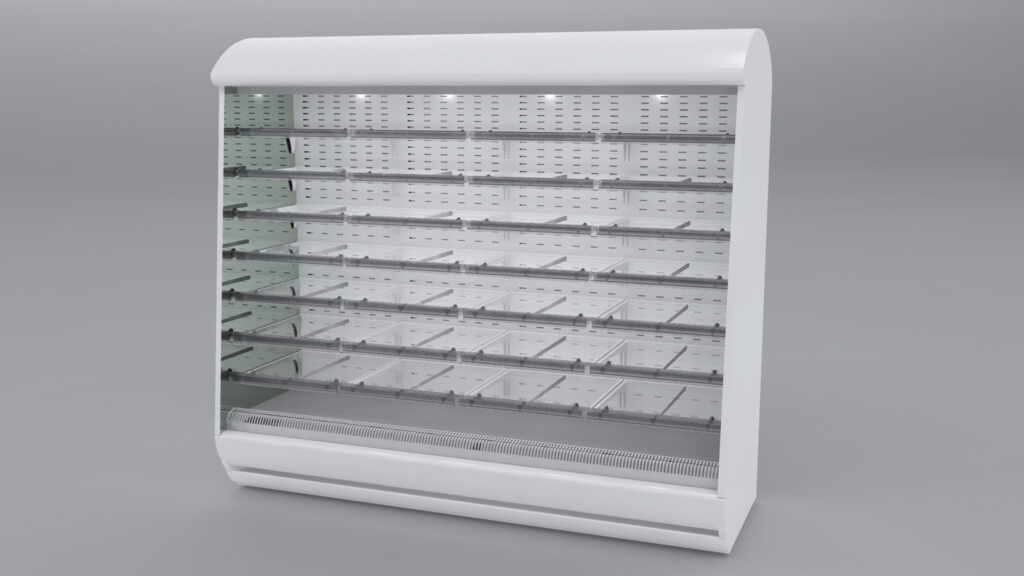
‘We work with cabinet manufacturers and make a detailed CFD model of their specific cabinet,’ explains Rowsell. ‘We then complete a full CFD analysis and optimize every aspect such as the size and location of the perforations in the back panel, fan speeds and sensor locations to improve energy efficiency.’
‘Along with the initial energy savings, there are a number of wider benefits as well,’ continues Rowsell. ‘The elimination of cold air spill from the cabinet reduces the heating requirements of the store and also allows smaller refrigeration plants to be used. Compounding the energy savings of our technology.’
The benefits of HELYX
The effective design of the EcoBlade and TrueChill relied heavily on utilising accurate CFD software. Wirth Research recently switched from using proprietary CFD tools to the open-source HELYX software from ENGYS. Yet, some of the results from NGR CFD simulations showed correlations within 1% of rigorous ISO [5] and ASHRAE [6] certification testing.
‘We quickly found that if we used our normal rigorous approach to geometry, meshing and tuning of the turbulence model, we could get the same results as proprietary software, but for a much more favourable licence fee,’ says Rowsell.
‘As we do a lot of work with heat transfer, buoyancy models are very important to us and this is an area where HELYX has much better models than OpenFOAM itself, making our solvers much more stable,’ continues Rowsell. ‘Our 17 years of experience and knowledge was easily transferred to HELYX and its intuitive architecture meant it was quick to pick up. But if we do need support, ENGYS are always on hand. We get all these benefits whilst spending orders of magnitude less than we were previously.’
References
[1] EIA/Shecco, 2018. Summary: Technical Report on Efficiency in HFC-free Supermarket Refrigeration, Environmental Investigation Agency
[2] Foster Alan, Brown Tim, Evans Judith, 2023, Carbon Emissions from Refrigeration Used in the UK Food Industry, Internation Journal of Refrigeration
[3] EIA, 2020, New Supermarket Study Underlines the Need to Put Doors on Fridges to Help Combat Climate Change, Environmental Investigation Agency
[4] John Lewis Partnership, 2021, Ethics and Sustainability Progress Report 2020/2021, John Lewis Partnership PLC
[5] ISO 23953-1:2023, Refrigerated Display Cabinets, International Organization for Standarization
[6] ANSI/ASHRAE 72-2002, Method of Testing Open and Closed Commercial Refrigerators and Freezers, American National Standards Institute
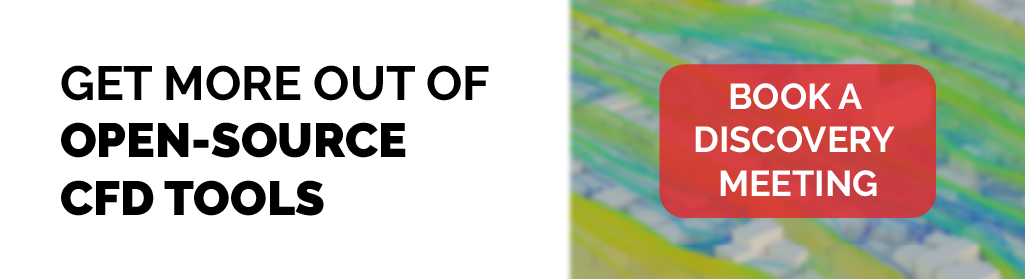