Enzo Ferrari famously said “Aerodynamics are for people that can’t build engines”. But in today’s efficiency driven world, aerodynamics is one of the most important development areas for OEM’s. New regulations demand vehicles to maximise fuel economy and minimise emissions, leading engineers to design aerodynamically efficient cars.
Digital WLTP
Following the diesel gate scandal of 2015, one of the most disruptive regulation changes hit the automotive industry; the Worldwide Harmonised Light Vehicle Test Procedure (WLTP). This global standard establishes a new driving profile, along with more relevant test conditions. It aims to consistently determine more representative fuel consumption and emission figures of passenger vehicles.
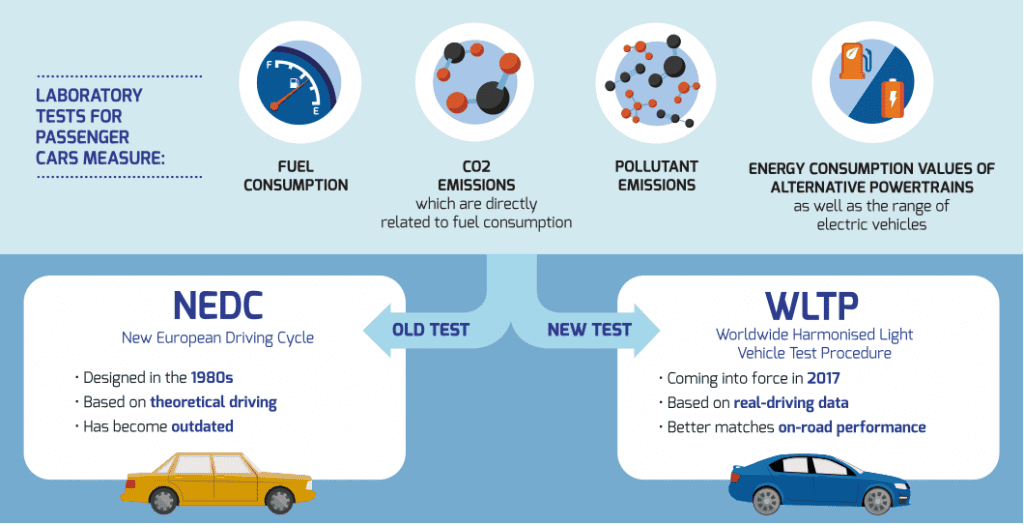
This new test regime is not only more stringent than previous procedures, but also requires every vehicle configuration to be tested. Consequently, alongside developing fuel-efficient and environmentally friendly vehicles, manufacturers also have to conduct intensive test programmes. With limited suitable testing facilities around the world, this can be a real challenge.
To alleviate some of these issues, WLTP offers a digital alternative, where OEM’s can provide CFD results to achieve certification. However, this requires manufacturers to demonstrate the equivalence and accuracy of their CFD processes to satisfy the WLTP. Therefore, automotive OEM’s need to have high confidence in their simulation capabilities.
CFD Benchmarking Study
To comply with the high accuracy required by the WLTP, Volvo decided to investigate the capabilities of five different CFD software’s [1]. Previous correlation studies had highlighted errors between physical testing and numerical methods. Therefore, Volvo wanted to determine the most reliable CFD code which could then be used for WLTP certification.
The numerical results from each code vendor were compared with wind tunnel data of a physical car. The air flow around a vehicle depends heavily on its dimensions. Consequently, Volvo used a range of reference cars including a Sedan, Estate and an SUV. In this way, it could evaluate the prediction quality of each code for the different flow phenomena of each vehicle type.
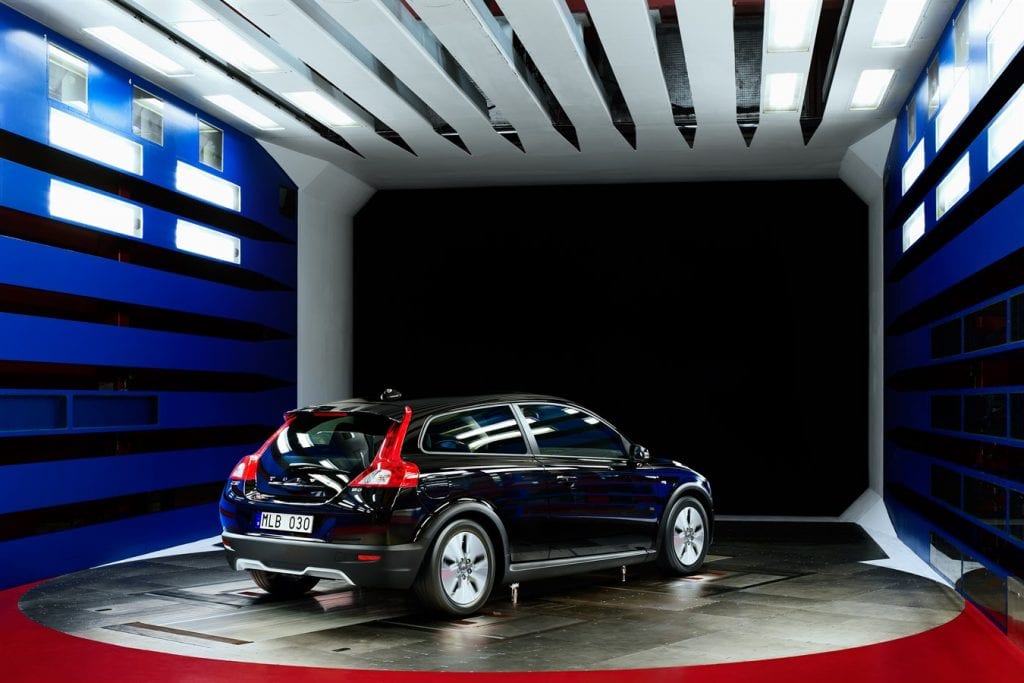
Each reference car was tested in Volvo’s wind tunnel which features a five-belt moving ground along with several boundary layer control systems. Both the physical and numerical tests were run at 0 degrees yaw and a wind speed of 140km/h. Drag, front and rear lift coefficients along with rear base pressure were measured in the wind tunnel and calculated in CFD. Wake plane measurements were also evaluated behind the front right wheel and the rear of each configuration.
The study was divided into three phases. The first required the code vendors to simulate the external aerodynamics of five different configurations of a Volvo V60 estate. The delta drag and lift forces were compared with wind tunnel data, as shown below.
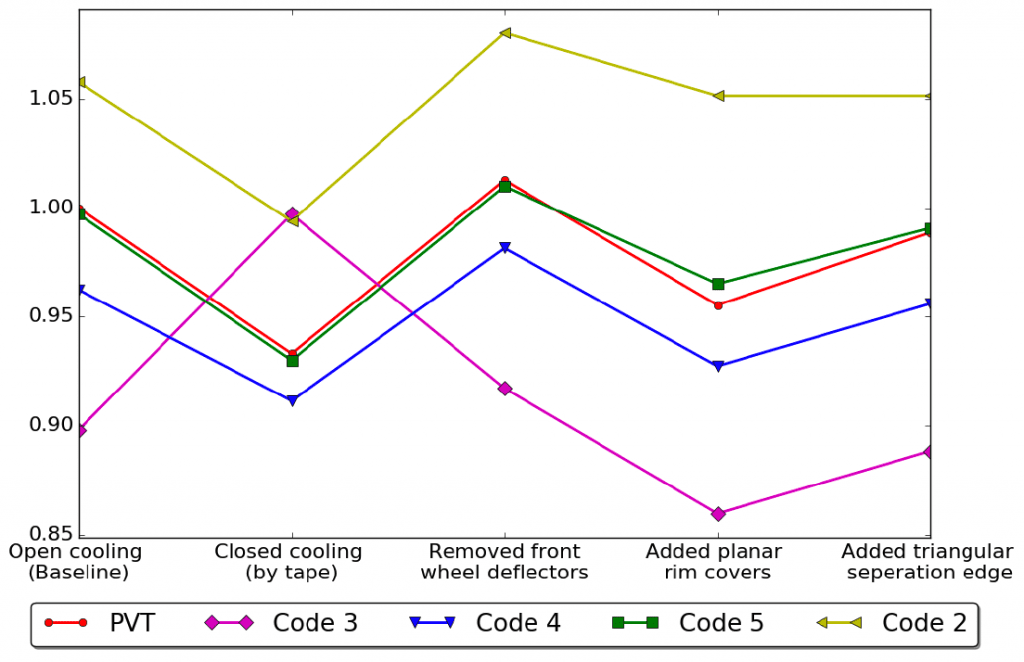
Code 5, which was ELEMENTS software from ENGYS, showed the strongest correlation with wind tunnel results. Consequently, Code 5 along with codes 3 and 4 were concluded to be the most accurate. These were then used in phase two where four variations of a Volvo S60 sedan were modelled.
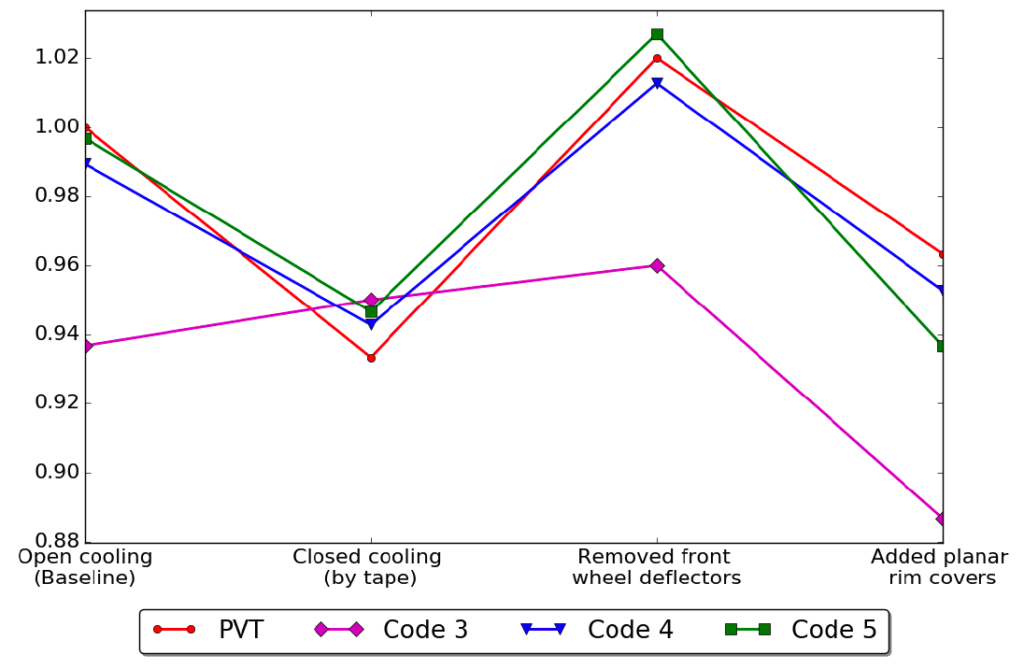
For the third phase, codes 3, 4 and 5 were then used to simulate five configurations of a Volvo XC90 SUV. Code 5 once again showed the strongest correlation with the wind tunnel.
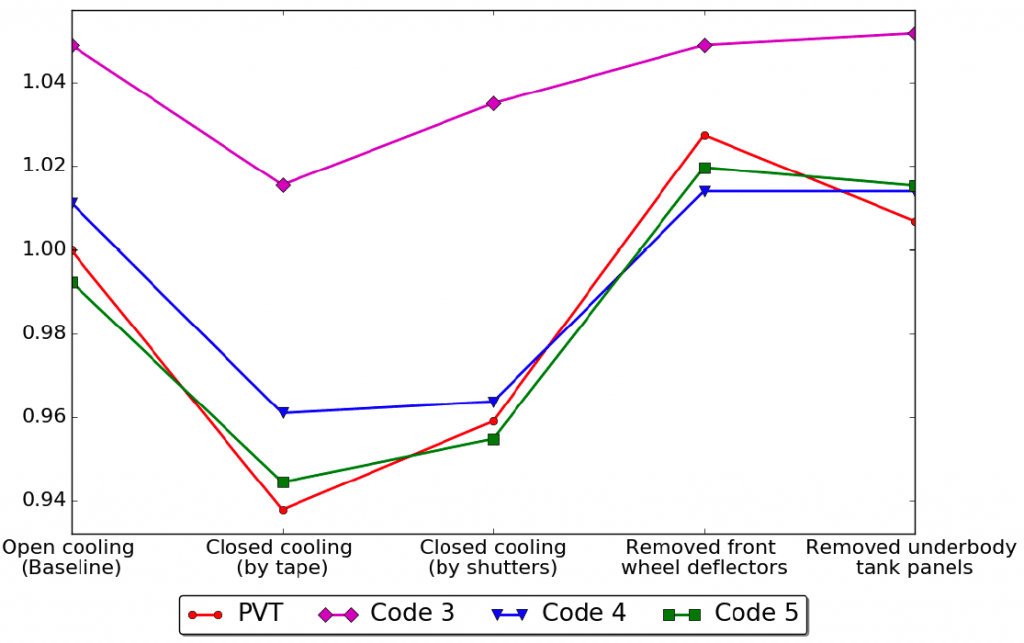
Throughout each phase, the deltas between aerodynamic coefficients were more important than absolute values. Volvo wanted to find a CFD package that could reliably predict trends, allowing engineers to easily evaluate the aerodynamic performance of design changes. Therefore, the optimum code had to show a strong correlation across all vehicle types. Lead times and simulation performance were also an important factor that Volvo considered.
Although each type of CFD software showed strengths and weaknesses, ELEMENTS was concluded to be one of the two top performers. This open-source CFD solution from ENGYS combines the best of automotive engineering design practices with the latest optimisation techniques. This gives manufacturers confidence in its results which show strong correlation with real data. That’s why Volvo selected ELEMENTS to model the aerodynamics of it’s vehicles for WLTP certification.
Reference Material
[1] Mattias Hejdesten and Simone Sebben. A CFD Benchmark for Improved Accuracy of Aerodynamics Simulations. 2017 JSAE Annual Congress (Spring) May 24-26 2017.
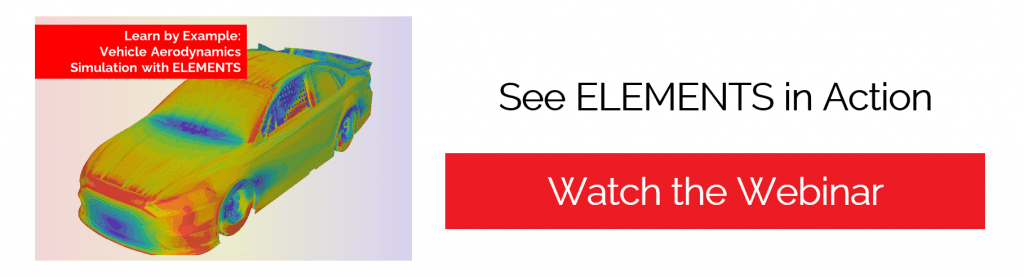