Over the last decade, automotive manufacturers have been continuously innovating new technologies, designs and approaches to maximise the fuel efficiency of combustion vehicles. This has led to an impressive 32% increase in fuel economy of new roadcars [1].
However, no matter how efficient a vehicle is, adding around 3,000Ibs (1,360kg) of trailer weight can increase fuel consumption by 50%. This is because the increased load of the trailer requires more power from the engine to travel the same distance. Consequently, every 100Ibs (45kg) of extra weight reduces fuel efficiency by 1% [2]. Over long distances, this can quickly accumulate and lead to double the fuel costs for drivers.
It gets worse with electric vehicles. Although on average there is a similar 50-65% loss in highway range between an electric vehicle and a combustion car, using an EV to tow a trailer presents other challenges. With much fewer charging stations than gas stations and recharge times taking two to four times longer than refilling a tank, long distance road trips can become unfeasible. ‘To help solve this problem, we wanted to develop the most efficient electric trailer on the market that can travel 300 miles,’ highlights Ben Parker, Co-Founder of Lightship, the company behind the revolutionary Lightship AE.1 Trailer. ‘This will help reduce the size of the powertrain required to tow the trailer and also neutralise its effect on battery range, offering a zero-range loss experience for drivers with electric vehicles.’
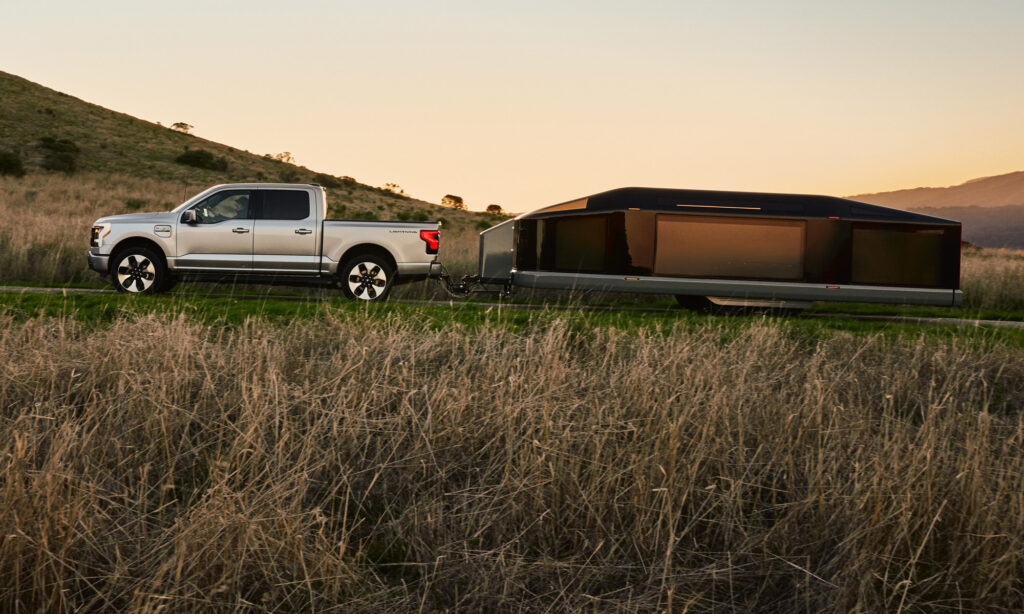
The Unique Design Approach of The Lightship AE.1 Trailer
Developing this innovative concept required a completely new approach to trailer design, thanks to Lightship’s automotive heritage. Typically, designers develop a trailer from the inside out. First, the interior living space is defined which then dictates the shape of the exterior. However, with Lightship’s priority on efficiency, the team focussed on designing an aerodynamically efficient shape first and then moved on to the interior.
‘It was clear to us early on that we needed to design the AE.1 from the outside in,’ highlights Parker. ‘First and foremost, this is a road going vehicle and from our automotive background we know that you have to design for efficiency right from the start, and that meant working on the exterior shape first.’
‘We also needed this shape to dictate the layout of the electric powertrain,’ continues Parker. ‘The AE.1 features its own motor and battery which allows it to propel itself, reducing the load on the tow vehicle and therefore significantly improving mileage and range. But with electric vehicles, the energy you can never recoup is the energy you lose to the wind, so to achieve our ambitious efficiency targets, we had to nail the aerodynamics.’
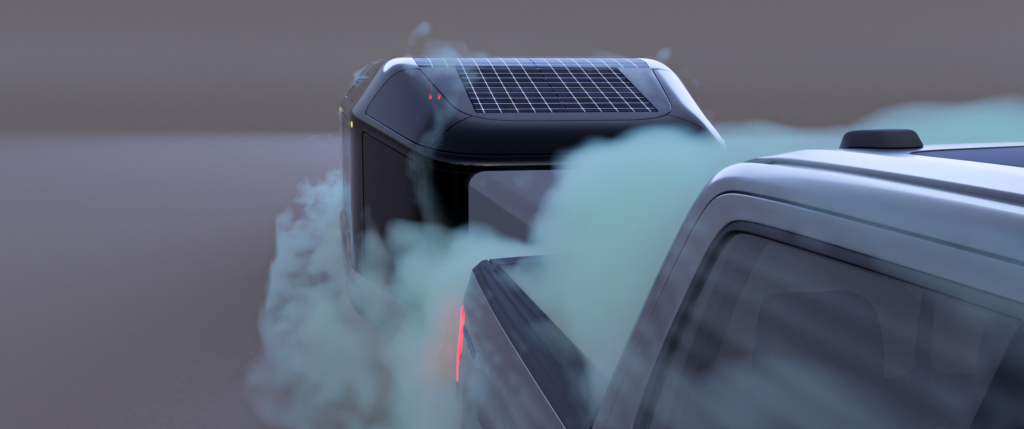
Reducing The Frontal Area
One of the key ways to reduce aerodynamic drag of an object is to minimise the frontal area. Travel trailers are typically large, tall boxes, so shrinking the frontal area presented a good opportunity for aerodynamic improvement.
‘To design a low profile shape, I proposed reducing the frontal area through telescoping, where the top of the trailer moves relative to the bottom,’ highlights Parker. ‘This led to the dual mode concept where in Camp Mode, the telescoping hard-sided walls extend upwards to increase the height and space of the trailer while stationary. Whilst in Road Mode, these walls collapse down, reducing the height and therefore frontal area when travelling.’
Boat-tailing The Rear
Another big effect on the aerodynamic performance of a vehicle is the wake. As air flows along the shape of an object, it slows down and eventually separates, forming a turbulent wake at the rear which increases pressure drag. To minimise this, smooth tapered profiles are used to keep the flow attached for longer and reduce the wake size.
Consequently, the most aerodynamically efficient shape is a teardrop, as the top and bottom surfaces eventually taper to a point. However, for a vehicle this would require an extremely long wheelbase which is not feasible for most vehicle designs.
‘The approach is different depending on whether you are designing the rear of a vehicle for drag or downforce,’ explains Angus Lock, General Manager at ENGYS North America who helped Lightship develop the AE.1. ‘For high performance vehicles, where downforce is the priority, then the optimum angle for the rear diffuser is around 8-10 degrees. But when designing for low drag, you either need to be much lower or much higher than that,’ continues Lock.
‘It is similar when looking at the rear profile, a rough rule of thumb in automotive is to keep rear profiles below 30 degrees from the longitudinal axis. Using steeper angles to try and aggressively reduce the size of the wake can actually induce strong vortices which then significantly increase drag. This is why we opted for shallower angles for the boat tailing of the trailer, but the trick was achieving this without consuming too much of the cabin space.’
To achieve this, it was decided to package protect a central portion of the cabin and ensure that the boat tailing could accommodate the width of a queen size bed. Furthermore, instead of optimising designs to achieve the lowest drag coefficient, other metrics such as CDA over volume were used to account for the interior. ‘This helped us achieve an aerodynamic design that maximised the volume on the inside when the trailer is expanded, but minimise the coefficient of drag when the trailer is collapsed,’ says Parker.
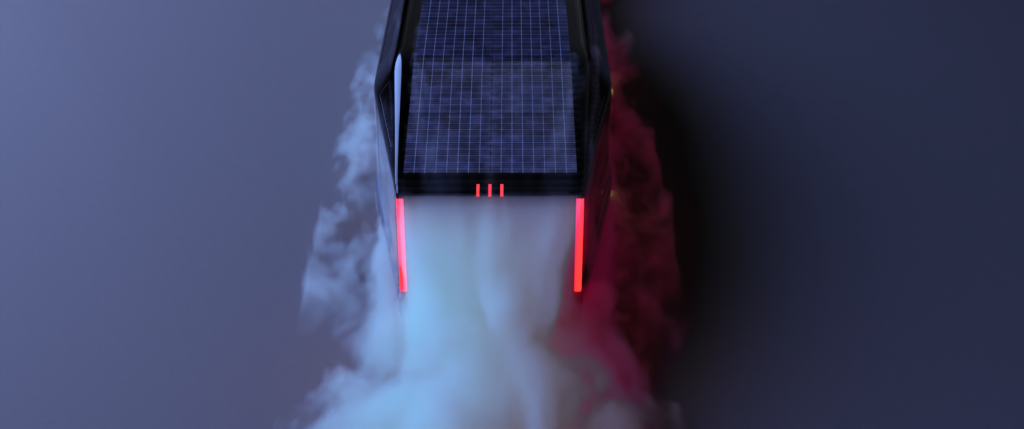
Morphing The Tongue Box
The most important part of any aerodynamic shape is the leading edge. This is not only the first point of contact with the airflow, but also dictates how the air interacts with the rest of the object downstream.
‘Initial CFD simulations in ELEMENTS highlighted how sensitive the aerodynamics of the trailer was to the shape of the nose,’ explains Lock. ‘One of the difficulties of designing a trailer is that it can be towed behind a myriad of different vehicles which significantly changes the condition of the oncoming airflow. So, we initially focussed on optimising the shape of the storage box on the tongue,’ continues Lock. ‘Most travel trailers have a storage box, but it is often quite small whereas we decided to shape the storage box to become part of the aerodynamic design. This helped to stabilise the flow around the front of the vehicle and reduce the differential between different types of tow vehicles.’
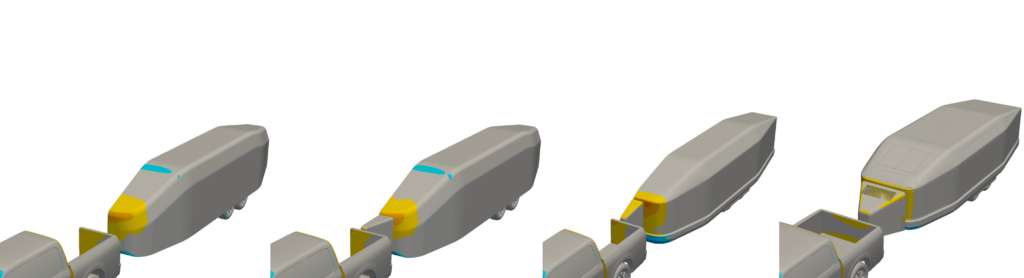
Streamlining Aerodynamic Trailer Concepts With CFD Simulation
Incorporating all these aerodynamic features together with optimising the overall package has helped the AE.1 trailer achieve a much higher aerodynamic efficiency than a classic travel trailer. This was only possible by taking a modern automotive aerodynamic approach and using comprehensive CFD tools such as ELEMENTS.
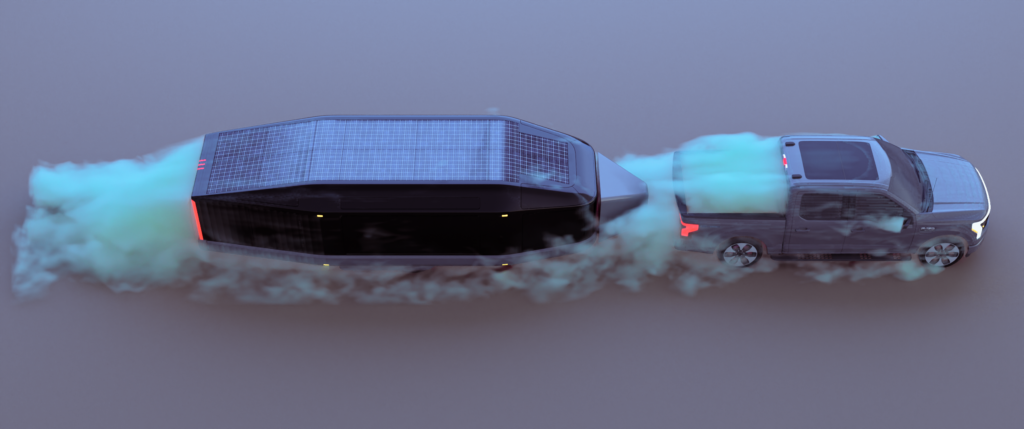
ELEMENTS CFD software allows users to model the external aerodynamics of vehicles within a virtual wind tunnel. After analysing the behaviour of the airflow around competitor trailers as well as some initial designs, Lock conducted a proportion study where key design parameters were identified and then optimised through a Design of Experiments (DOE) approach. This not only established the optimum of each of these parameters, but also the sensitivities of these parameters to different shapes; helping steer the design team towards the final concept.
‘Using the power of simulation, we could rapidly change the shape of the vehicle and understand the effect on drag, which would be very challenging and costly to do in a wind tunnel,’ highlights Lock. ‘We also considered the aerodynamic behaviour at different yaw angles as sometimes the wind loadings can be huge. But with the low roof angle and the shape of the sides, the AE.1 has great stability in crosswind scenarios compared to traditional travel trailers.’
The major benefit of ELEMENTS software is that it is extremely efficient. In fact, for transient simulations it is 2 to 3 times faster than most traditional CFD packages, which is why 60% of the current Formula 1 grid utilise it. This efficiency helped Lock to turnaround simulation results quickly and cost-effectively which allowed a broad assessment of the design space, which is key when developing such a revolutionary concept.
‘The team at ENGYS did a year of aerodynamic development work before we had any design input,’ says Parker. ‘Without this, we wouldn’t have been able to achieve the efficiencies that make the AE.1 a cost competitive vehicle, it simply wouldn’t exist.’
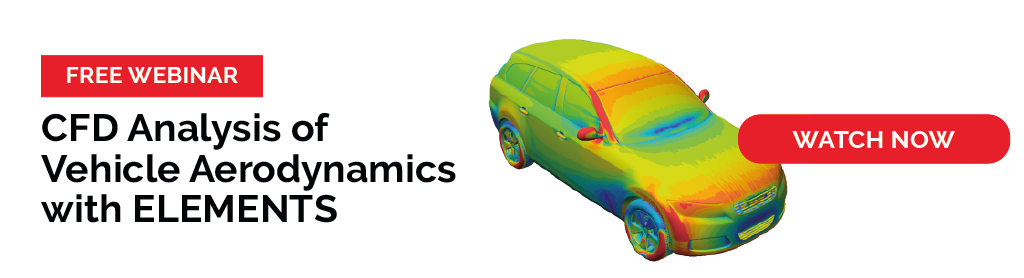
References
[1] Highlights of the Automotive Trends Report [Online]. United States Environmental Protection Agency
[2] A.C., R.B., 2007. Impact of Vehicle Weight Reduction on Fuel Economy for Various Vehicle Architectures [Online]. Ricardo