Artificial Intelligence (AI) coupled with traditional Compute Aided Engineering (CAE) tools provide the potential of transforming the engineering design process. This is one of the driving forces behind the UPSCALE Project, specifically applied to the future design of electric vehicles. The EU project is a collaboration of several industrial and academic partners, where ENGYS is developing components for work package 1 “Machine Learning Enhanced Simulation Tools”. Overall the goal of work package 1 is to enhance the performance of existing CFD tools using machine learning and model order reduction.
The accessibility of powerful compute capabilities; the development of machine learning software libraries; and the growing need in industry to augment human decision making has given rise to the development of practical uses of AI. For the automotive industry, there is a need to balance aesthetic design, with the engineering performance of the vehicle (e.g. drag and lift). This balance is achieved traditionally through feedback from stakeholders within engineering and design teams to drive towards a conceptual and final design. Any effort to reduce iterations and achieve the goals of stakeholders results in tremendous savings in both time and money. With machine learning and computational fluid dynamics (CFD) coupled tools, there is the potential to lower overall costs via leveraging training data ( e.g. previous CFD runs ) and intelligent flow feature prediction.
The application of machine learning to aero-thermal design was outlined in a recent interview on the upscale website, highlighting several key project developments in order to:
- Enhance standard aerodynamic solvers with ML to speed up pressure projection so that they can be used to generate training data for the real-time models more quickly
- Improve the accuracy of RANS turbulence models to provide the same accuracy as high-fidelity methods like LES/DES for a fraction of the cost
- Configure the training system that will allow neural networks to predict the flow field around electric passenger vehicles in real time
The implication of these developments reach beyond automotive applications, affecting nearly all virtual prototyping processes using CFD simulation. Ultimately, it’s about using past experience (training data) to predict meaningful results on a new design scenario. These developments, along with an overview of of how ENGYS is creating tools related to machine learning and CFD are the subject of a recent webinar.
Learn More by Watching the Webinar
Eugene de Villiers presents the ongoing work by ENGYS developers and engineers within the UPSCALE project and how that relates to future improvements in Aero-Thermal design in the automotive industry. Attendees will be able to see some of ENGYS’ research and development activities and ask questions about the cutting edge work sponsored by the UPSCALE project.
Click the banner below to access the webinar.
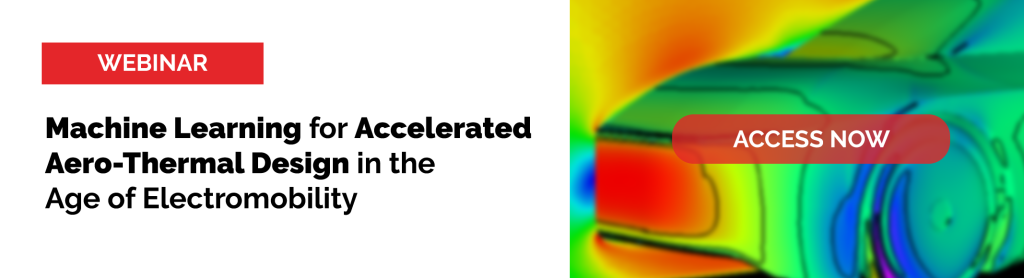