In the United States alone, individuals use an average of 88 gallons of water a day within their home [1]. Delivering that tremendous quantity of water involves a complex system of valves, pumps, and piping systems, each with their own engineer problems to solve. Conservation of potable water and reduction in energy usage to deliver fresh water to households around the globe, is an especially important design goal for faucet manufacturers. In Brazil, DOCOL is a leading faucet design and manufacturing company, with a mission to support water-saving through design, comfort, quality, and technology while creating value for society. Part of their strategy to achieve these goals is prototyping and testing, activities well-known to DOCOL, since they operate an advanced hydraulic laboratory equipped to test new designs [2]. To evaluate the benefits of HELYX, ENGYS and DOCOL completed a “proof of functionality” project to showcase how HELYX and HELYX Adjoint (Continuous Adjoint Approach) could enhance DOCOL’s virtual prototyping capability through CFD simulation and optimization. Ultimately, incorporating HELYX Adjoint in the design process could improve current faucet designs to reduce pressure losses and reduce material usage to bring down manufacturing costs.
Optimization Results At a Glance
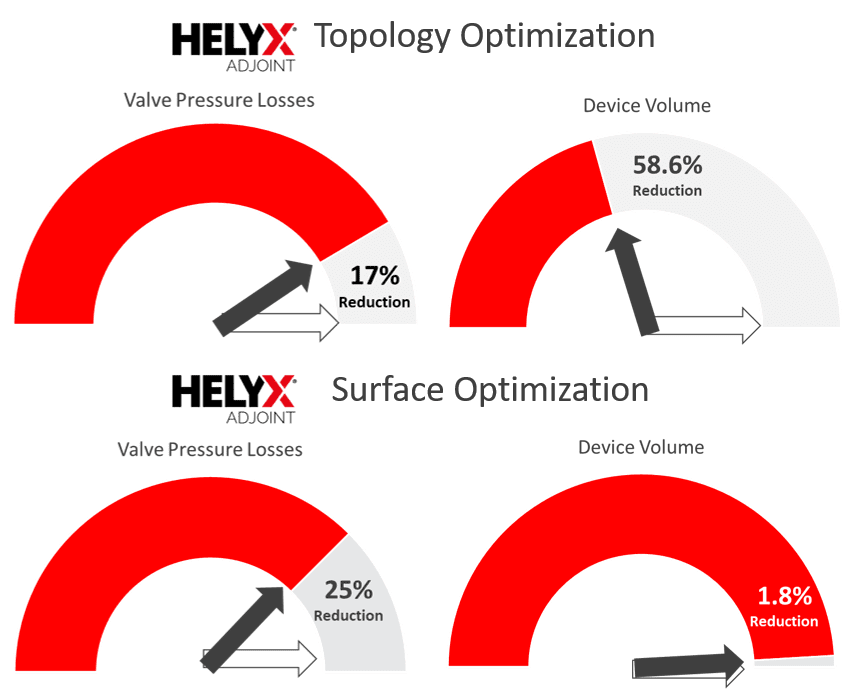
The Challenge: To selectively optimize regions of a faucet valve, given multiple engineering objectives
DOCOL engineers wanted to see how HELYX and HELYX Adjoint could improve their current faucet designs to:
- Reduce material usage to bring down manufacturing costs and material waste while still maintaining desired flowrates
- Reduce the pressure losses to create a more energy efficient product
- Maintain the current valve mechanism design to not require further work from engineers
- Maintain manufacturability of the device to ensure that the current manufacturing process is still used e.g. not require 3D printing
Overall, the goal of the optimization study was to augment the efforts of DOCOL engineers to increase product performance in the design shown in Figure 2 and add value for their customers, given multiple engineering, design, and business objectives.
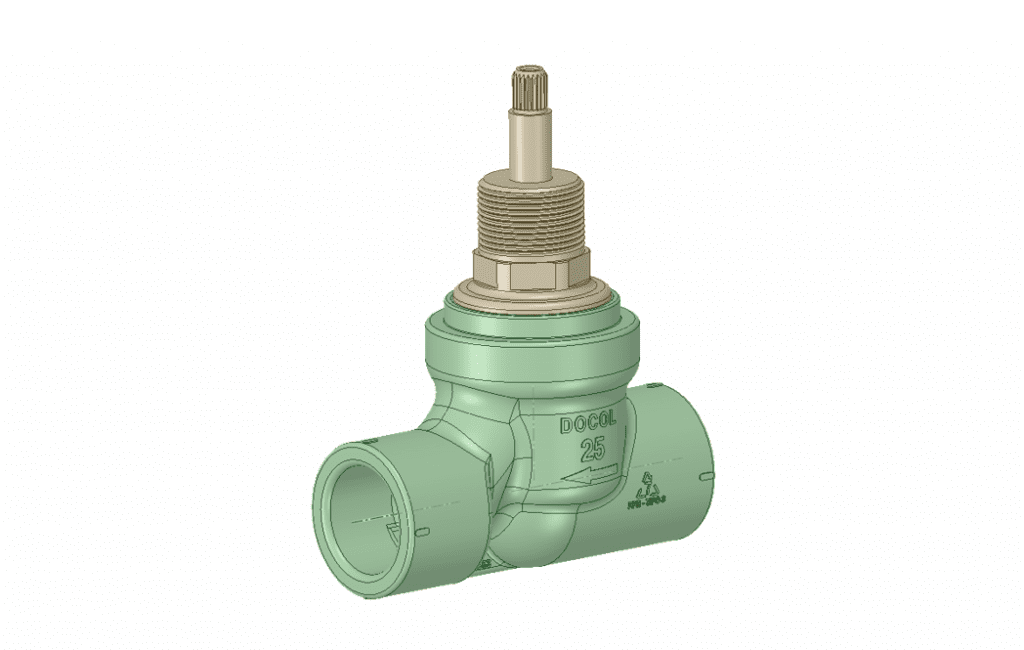
The Solution: Perform an optimization analysis and automatically create new design surfaces
For a product that has years of engineering design, laboratory testing, and customer success behind it, developing a new and optimized valve design can be a difficult process. Using HELYX Adjoint, DOCOL engineers could gain deeper design insight into structure-function relationships of their valve’s performance. One key requirement is that only the inlet and outlet paths of the valve can be changed, and it was essential that the inner valve mechanism remain intact (Figure 3).
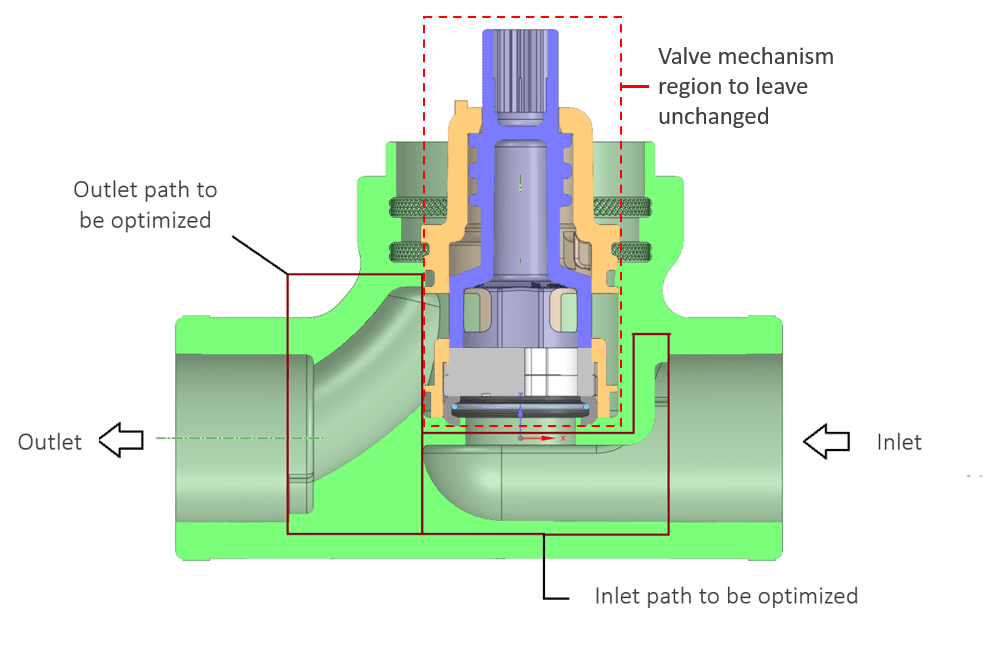
To perform this optimization, two complementary approaches were used to determine an optimal shape of the inlet and outlet valve regions:
Topology Optimization Evaluation
A 315k cell mesh (Figure 4) was constructed within HELYX to represent the maximum design envelope allowed for the valve. Within the static mesh, an optimal surface evolves based on the design objective sensitivities, determined by the continuous adjoint algorithm. Engineers perform steps very similar to a steady CFD analysis of a valve and specify boundary conditions (walls, inlets, outlets), turbulence models ( realizable k-epsilon in this case), numerical schemes (second order schemes), design objectives (pressure loss minimization), and topology optimization settings (surface evolution settings). Engineers then specified that only inlet and outlet flow regions in Figure 3 could allow an evolved topology. Once the optimization begins, the optimal surface evolves from the walls themselves to produce a design surface to meet the user-specified objective.
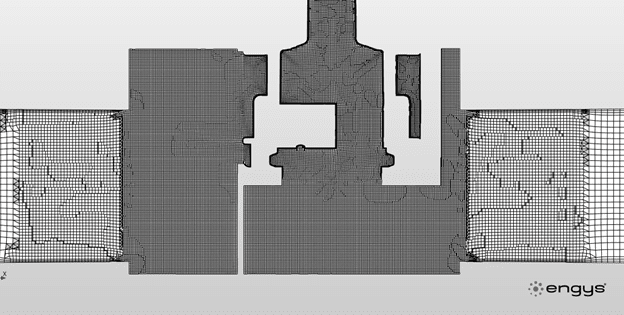
Surface Optimization Evaluation
In the surface optimization evaluation, the current design surfaces were deformed to minimize a pressure loss objective. These small deformations are captured in a 275k cell mesh created directly within HELYX (Figure 5) and setup similarly to a topology-based optimization. The main differences is that In a surface-based optimization, engineers specified constrained and movable boundaries to prevent or allow boundary deformation. In this case, only allowing the inlet and outlet flow regions shown in Figure 3. Once the optimization begins, the user-specified boundaries and connected volume mesh morphs to produce a design surface to meet the pressure loss objective.
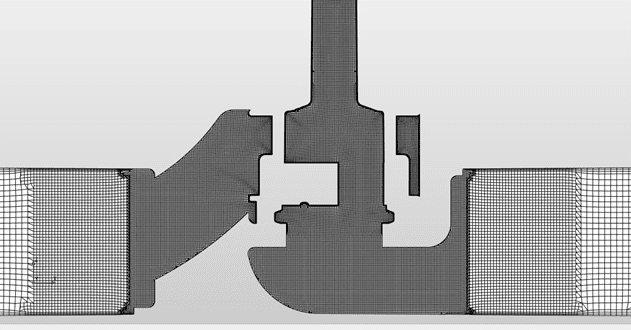
The Outcome: A design resulting in reduced pressure losses, reduced material usage, and consistent design aesthetic
DOCOL engineers saw that both the topology and surface-based optimization offered suggestions to an improved the valve design. Through topology optimization, a reduction in pressure losses of 17 percent compared to the original design and a component volume reduction of about 58.60 percent was predicted. This was performed over a 10-hour analysis on a 12-core workstation. Figures 6A and 6B show the evolution of the optimal surface as the pressure losses are minimized.
Figure 6 A: Top view of topology optimization of valve, showing optimal shape forming over the optimization process
Figure 6 B: Side view of topology optimization of valve, showing optimal shape forming over the optimization process
Through surface-based optimization, a 25 percent decrease in pressure losses compared to the original design and a 1.86 percent decrease in volume was predicted. This was performed over an 8-hour period on a 12-core workstation. Figures 7A and 7B show the evolution of the surface morphing to reduce the pressure losses.
Figure 7 A: Top view of surface optimization of valve, showing optimal shape forming over the optimization process
Figure 7 B: Side view of surface optimization of valve, showing optimal shape forming over the optimization process
The Implication of Continuous Adjoint Results
- Both topology and surface optimization approaches predicted reduction in pressure losses and a reduction in device volume at given target flow rates.
- Both topology and surface optimization approaches were able to selectively optimize regions of the device without modifying the engineered valve mechanism.
- Beyond the immediate results, there is a gained knowledge of the direct connection between an optimized shape and the objective value (pressure loss) to quantify the actual result of the changes predicted by HELYX Adjoint. This helps engineers predict the impact of the suggested changed of the shape with the cost needed to make minor changes in the faucet manufacturing process.
- There is direct feedback to engineers on the influence of structure and shape within the faucet system i.e. what topology changes lead to better faucet performance. This improved outlook enhances their “design intuition” when looking at organic shapes that may have not been previously explored.
- The valve mechanism was untouched by both the evolving optimal topology and the morphing mesh, making implementing the resulting shape more appealing and less expensive to manufacture
- DOCOL engineers could use the optimal results to augment their decisions for future faucet designs
Your Next Steps
Schedule a discovery meeting with ENGYS to see if your products and scope of physics are a good candidate for adjoint optimization. If they are, we can work together to perform a “Proof of functionality” project and help you and your team evaluate the benefits of HELYX and HELYX Adjoint.
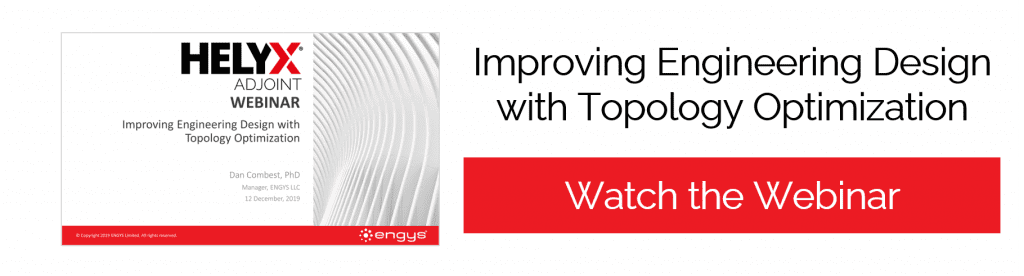