The automotive industry is currently enduring one of its most challenging periods to date. Manufacturers need to develop lighter, cheaper, more efficient vehicles whilst dealing with chip shortages, rising costs and the continued debate around powertrain technologies. This has demanded innovation and in 2020, €58.8 billion was invested in automotive R&D in Europe alone, the world’s largest investor in innovation in the automotive industry.
To maintain this rate of development, automotive manufacturers need to rely on accurate simulation tools that are easy to use and can iterate through solutions quickly and efficiently. Computational Fluid Dynamics (CFD) is one of these tools and has revolutionised how aerodynamicists can optimise the aerodynamic performance of vehicles.
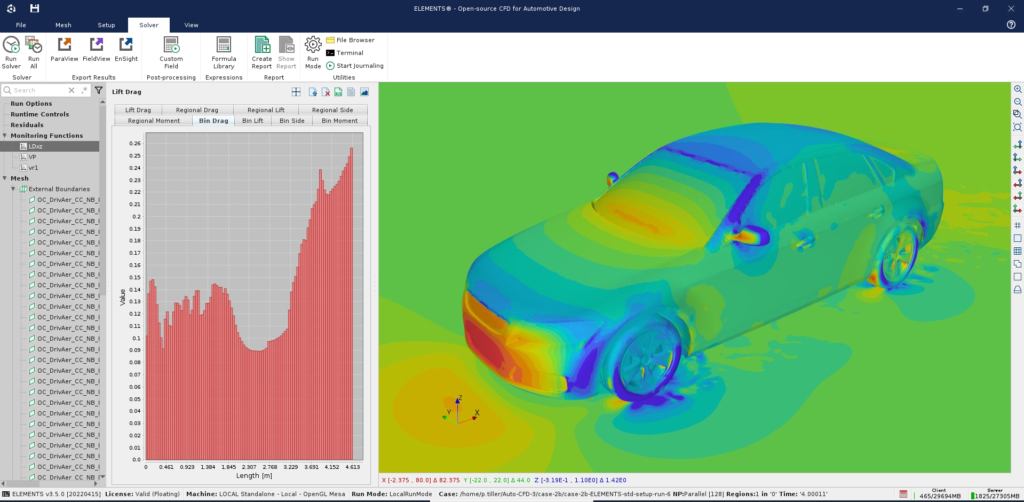
Accessible CFD Software
Yet despite its growth, CFD still requires a high level of expertise to navigate the complexities of meshing, solver settings and turbulence modelling to achieve accurate results. To help solve this problem, ENGYS have incorporated best practices and CFD simulation templates into its CFD software, ELEMENTS.
ELEMENTS is a software package specifically developed for the automotive industry. It is based on ENGYS’ own open-source CFD simulation engine and the same GUI technology delivered as part of HELYX. ‘Our focus with ELEMENTS was to make it easy for an aerodynamicist without in-depth CFD knowledge to come up with a full CFD analysis with accurate results for lift, drag and balance,’ explains Thomas Schumacher, Director and co-founder of ENGYS.
‘To achieve that, we created a set-up wizard which displays a selection of simulation templates or best practices. The user simply imports the geometry, defines the overall parameters such as how the wheels and heat exchangers should be treated and then selects the most relevant template for their study. This streamlines the set-up phase because users don’t have to adjust the mesh settings, volume refinement settings or turbulence models.‘
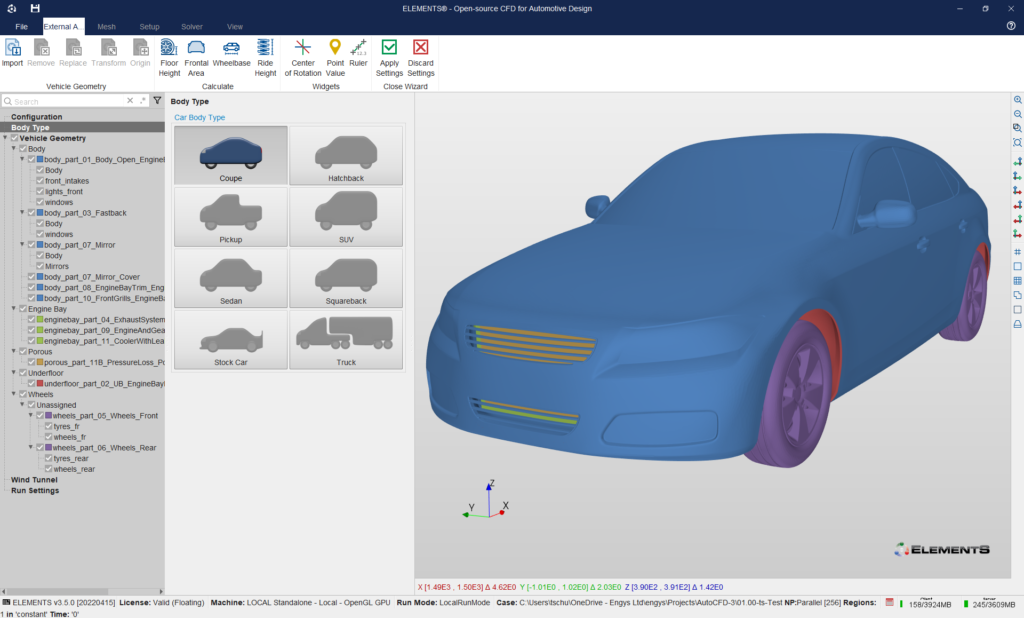
CFD Simulation Templates
Within ELEMENTS there are a variety of simulation templates, each tailored to a specific type of vehicle and wind tunnel. The template defines characteristics such as mesh settings and solver parameters, which are based on real world data.
Find out how ELEMENTS compares with other CFD solvers in this automotive benchmark study
‘We conducted an extensive wind tunnel campaign using ARC’s [Automotive Research Centre] scale model wind tunnel,’ highlights Schumacher. ‘We ran a case matrix of dozens and dozens of different vehicles and vehicle types. Using all of the literature and experimental data we could find, we optimised our CFD solver settings and models to give excellent results for each simulation template.’
Standardisation and Customisation
The standardisation of these simulation templates helps aerodynamic departments improve their CFD workflows, particularly when integrating new engineers into the team, or when switching to ELEMENTS for the first time. However, traditional OEMs have years of expertise bound up in their own CFD methodologies so may not want to abide by these standard templates.
‘Often OEMs will have their own methods development department, so it’s important for us to give them the freedom to create their own templates,’ explains Schumacher. ‘The CFD experts within the company can create custom buttons that contain their own best practice settings for meshing and solvers. The aerodynamicists, who may not be CFD experts, can then run ELEMENTS with the confidence that when they select a simulation template, it applies their company’s best practice for that vehicle.’
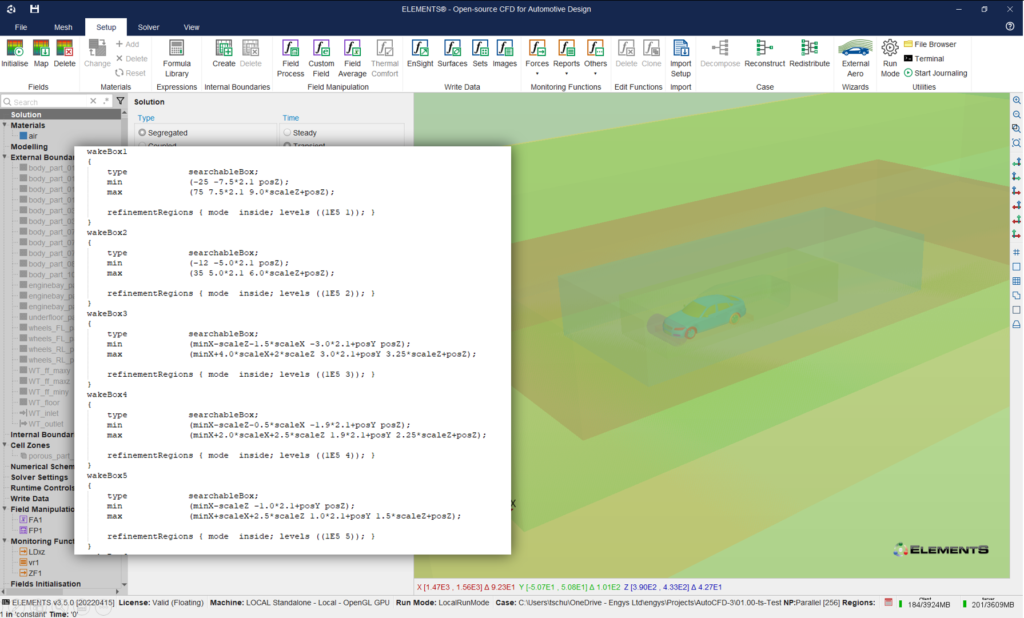
‘I think this approach is unique to ELEMENTS and one of its distinguishing features,’ Schumacher continues. ‘We can run standard or customised templates, ensuring each aerodynamicist runs cases with the same turbulence settings or the same mesh. It’s also fast in terms of turnaround times and uses an open-source base, so has no additional HPC costs.’
The capability to develop your own templates has been particularly beneficial for the automotive industry of today which is becoming ever more varied. From new EV start-ups that are disrupting traditional OEMs, to manufacturers creating high performance, low volume hypercars, working with ENGYS and ELEMENTS can be perfect for their business model and staffing levels.
Find out how to conduct a CFD analysis of a vehicle’s aerodynamics
‘For these new companies or projects, the best practices may not be defined yet,’ says Schumacher. ‘We can work with them to put these in place and create or modify templates to fit their specific requirements. This is how ENGYS became involved with Koenigsegg on the Jesko Absolut project.’
The Jesko Absolut
Koenigsegg have been creating low volume hypercars since their inception in 1994. The Jesko is their latest creation with a track-specific version known as the Attack and a further development called the Jesko Absolut.
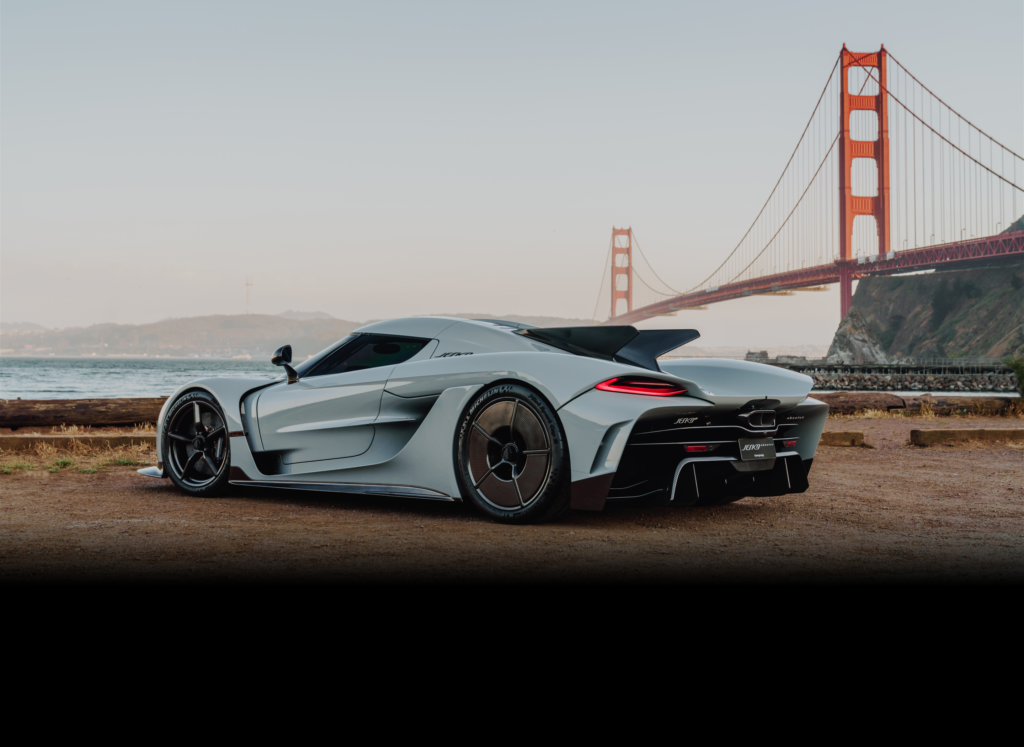
Figure 4: The Jesko Absolut aims to be the fastest Koenigsegg ever produced. CREDIT: Koenigsegg.
‘The goal with the Jesko Absolut was to create the quickest Koenigsegg the company will ever produce,’ reveals Harry Kounenis, Aerodynamic Team Leader at Koenigsegg. ‘It’s essentially a high-speed version of the Jesko Attack and will attempt to break the 500kph speed record. This makes it a very unique project in terms of external aero simulations as exceeding 500kph results in Mach numbers greater than 0.3. This is considered the threshold where compressibility effects must be considered.’
‘Compared to the more usual incompressible fluid flow assumptions, there may be differences in density and pressure,’ continues Kounenis. ‘Therefore, the areas of separation and stagnation may change, resulting in different boundary conditions and wakes.’
Find out more about the Jesko Absolut
Simulating the Jesko Absolut (It can’t be that hard!)
Koenigsegg are used to creating high performance vehicles, but the requirements of the Absolut meant that new CFD methods were needed. Together with the engineers at ENGYS, Koenigsegg were able to create a bespoke ‘supercar’ simulation template in ELEMENTS, specific to the Absolut, but there were plenty of challenges along the way.
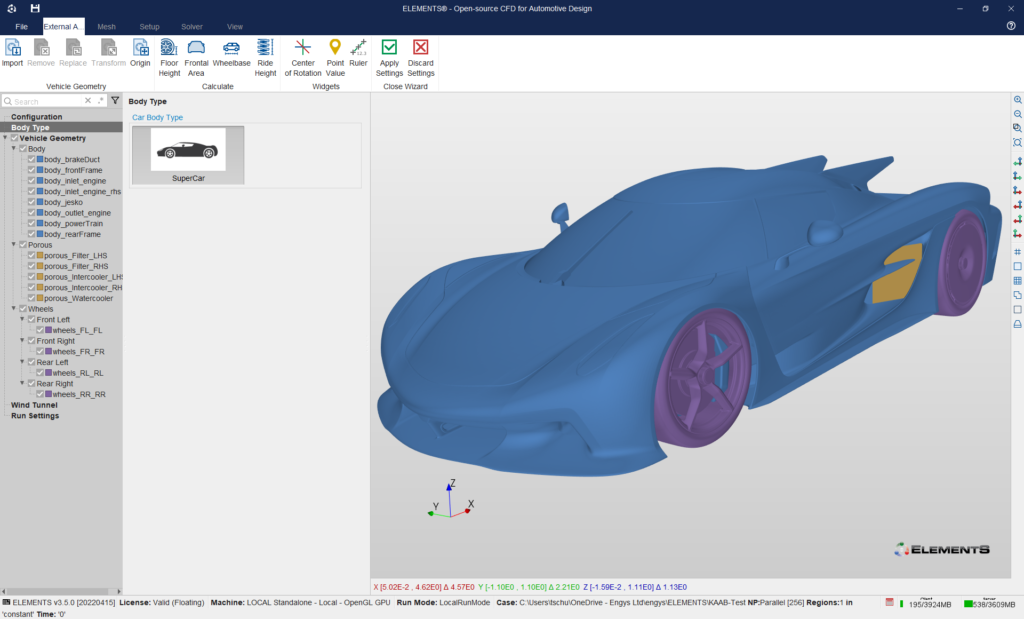
‘The industry standard for road car CFD development is 140kph, whereas at 500kph compressibility effects can’t be neglected,’ highlights Schumacher. ‘To achieve accurate results, we had to ensure that our template was robust and flexible enough to run behind the scenes with a different solver setup which accounts for compressibility. We also wanted to still use detached eddy simulation [DES] for best accuracy.’
‘Furthermore, the car has large diameter five-spoke rims, which requires a moving mesh to allow the rims to rotate,’ continues Schumacher. ‘We’ve done these things in the past so we felt we could meet each individual requirement, but it was an interesting challenge.’
Meshing Approach
As with all CFD projects, producing an accurate yet computationally efficient mesh was important, particularly for the unique characteristics of supercars. The helyxHexMesh extrude mesher algorithm with 100% layer coverage was used. The final mesh totalled more than 90 million elements.
‘The stagnation area on the nose of a supercar sits a lot lower than on a normal passenger car,’ explains Schumacher. ‘Everything on a supercar is more aggressive and streamlined in the pursuit of downforce. This generates upwash which changes the mesh required to capture the shape of the wake. Accounting for low profile supercars required tweaks to the mesh settings, but that was easy as that’s exactly what the template is for.’
Results
Identifying the project-specific settings and creating a new template to suit, is only the beginning of the challenge. Achieving accurate results from simulations that can then be used to answer development questions, particularly those relating to compressible fluid flow regimes, was the next task.
‘We approached the problem in two ways,’ highlights Kounenis of Koenigsegg. ‘The first was to run a steady-state simulation with some compressible settings. The second was a full unsteady simulation, which is always more difficult and time consuming. In the end, the results were quite similar, allowing us to use the faster simulation set up whilst remaining confident with our results.’
Koenigsegg was also able to establish that the centreline symmetry was sufficient to allow them to test one half of the car for straight-line, high-speed conditions, saving meshing and computational time.
CFD Based Design
Along with aerodynamic development, CFD results can also contribute to a better structural design. ‘As you can imagine, at those speeds there are a lot of structural effects,’ adds Kounenis. ‘These CFD simulations allow us to produce pressure maps for the FEA group so that they can generate stress load cases for components and closures. This is particularly important at such high speeds, as you don’t want to have anything flying off the car.’
Animation 1: Total pressure isosurfaces around the Jesko Absolut.
Overall, the combination of standard templates along with the flexibility to develop bespoke templates, has helped Koenigsegg with its aerodynamic development programme of the Absolut as well as its other vehicles.
‘We are in the building phase of our CFD team and processes,’ concludes Kounenis. ‘Using ELEMENTS has led to a huge improvement in our workflows and repeatability. There is also potential to improve our CFD using the supplied templates within the software and carrying out further modifications as we learn. We now use ELEMENTS for our standard external aero development across different programmes and vehicle shapes.’
‘ELEMENTS is simple to use, especially for people new to the software,’ Kounenis continues. ‘There is very good support from ENGYS who always provide quick answers which is essential in our environment where things move relatively quickly. You get responses within a few hours instead of waiting days before you can progress and submit your simulations.’
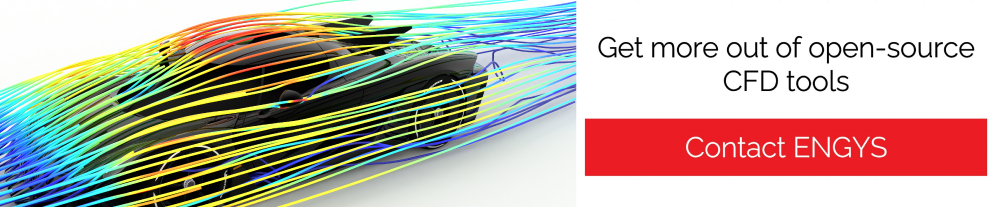