Home » Automotive
Automotive
HELYX and ELEMENTS are trusted by leading automotive OEMs and suppliers worldwide. Our open-source CFD solutions offer unparalleled scalability, empowering you to accelerate product development and bring new products to market faster than ever before.
EXCEPTIONAL VALUE
How are automotive engineers benefitting from our open-source CFD solutions?
No more limited cores
The open-source nature of HELYX and ELEMENTS enables you to fully leverage your own hardware by running simulations in as many computer cores as you have available, without having to pay costly additional HPC licenses.
No more waiting in line
Traditional CFD software often forces you to wait for one simulation to finish before starting another, unless you pay for costly HPC licenses. With HELYX and ELEMENTS, there are no such constraints. Run multiple simulations simultaneously and handle pre- and post-processing tasks without delay.
True high-fidelity CFD
ELEMENTS, our tailored CFD solution for automotive design applications, ensures precision through best practices and custom scripts, allowing you to optimize designs for maximum aerodynamic efficiency and performance. These practices have been validated against experimental data from several real wind-tunnel tests.
engys products
Discover our open-source CFD solutions

Tailored CFD software for automotive design
ELEMENTS is an open-source CFD software tailored for external aerodynamics analysis and vehicle flow design applications. ELEMENTS combines two simulation environments in one package: a dedicated virtual wind tunnel wizard for modelling external vehicle aerodynamics, and a general purpose CFD interface for solving other vehicle design applications.
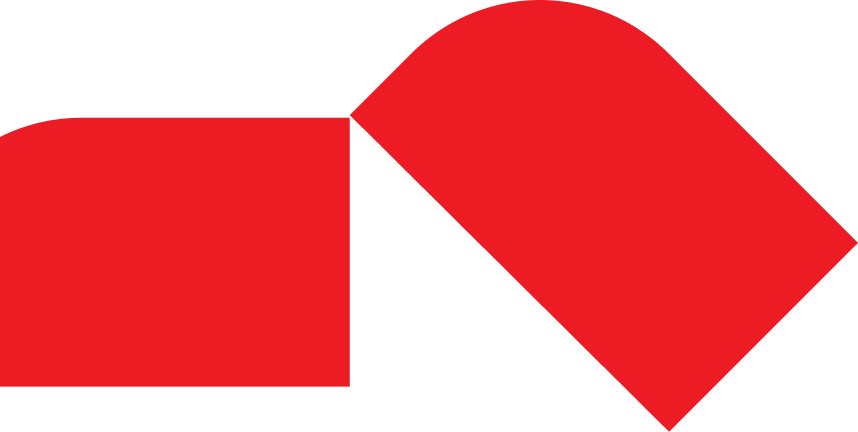
Learn how our open-source CFD solutions were used to design the most aerodynamic travel trailer.

General-purpose, open-source CFD software.
HELYX is a general-purpose, open-source CFD software used by many OEMs and suppliers to solve a wide range of automotive applications, such as UHTM, external aerodynamics, HVAC and cabin comfort, battery cooling, brake cooling, and aeroacoustics.
partner products
Discover our partner’s AI product
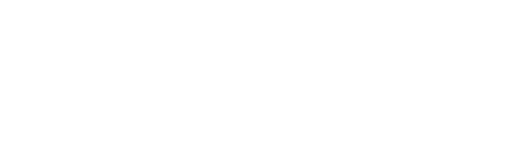
Explore better designs faster with AI.
NavPack AI-accelerated interactive design solution integrated into many automotive OEMs engineering workflow is enabling the automotive industry to explore better designs faster.
AUTOMOTIVE APPLICATIONS
Industry leading technology.
Unlimited license scalability.
Unmatched value.
CONTACT US
Contact our team of CFD experts.
Consent Notice
By submitting your request, you agree to be contacted by email to receive important announcements from ENGYS, including new software releases, product updates, sponsored events and company news.